Introducing AlignUp!: Revolutionary Trucking Assignment Optimization
We are thrilled to release AlignUp!, a powerful new feature that transforms trucking lineup assignment for contractors. AlignUp! is designed to minimize truck travel distance while respecting all constraints, saving time, reducing risk, and increasing adaptability to last-minute changes, providing immense value to your organization.
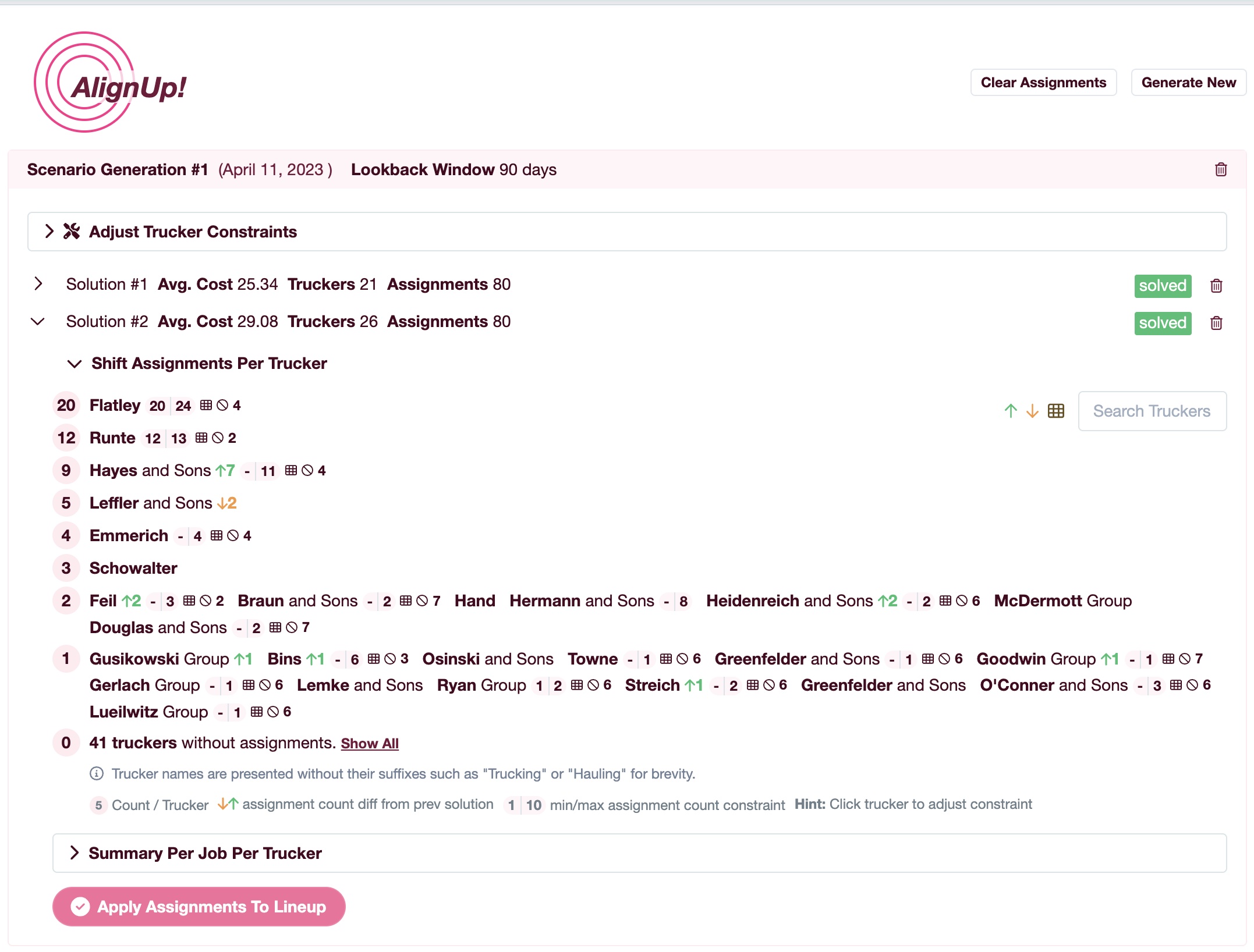
Why AlignUp! Matters
- Increased Construction Planning Time: By automating the lineup assignment process, less time is reserved for dispatch, allowing your team to focus on other essential aspects of construction planning.
- Responsive to Late Changes: AlignUp! adapts to last-minute schedule changes, ensuring efficient resource utilization even in uncertain situations.
- Minimized Travel Distance: AlignUp! intelligently considers trucker locations and finds the best use for each trucker, reducing travel distance, saving fuel costs, and time.
- Reduced Risk: AlignUp! makes it possible for any team member to optimize and dispatch a lineup, ensuring smooth operations even when someone is on vacation, or when there is turnover.
- Dealing with More Truckers: By keeping track of every trucker's location and capabilities, AlignUp! makes it easier to manage a larger number of truckers and scale operations.
Key Features of AlignUp!
AlignUp! optimizes trucking assignments to minimize travel distance while respecting various constraints, offering unique functionality including:
- Efficient Scenario Generation: The initial scenario generation for over 100 shifts and 50+ truckers takes less than 1 minute, while subsequent solutions with adjusted constraints are generated in less than 30 seconds.
- Trailer Classification Requirements: AlignUp! matches trailer classification requirements (including equivalencies) to ensure truckers are assigned appropriate tasks.
- Minimum and Maximum Assignment Counts: The system considers minimum and maximum assignment counts per trucker, optimizing resource utilization.
- Material Type Constraints: AlignUp! incorporates material type constraints, ensuring that truckers are assigned to tasks suitable for their equipment and preferences.
- Intelligent Constraint Defaults: Based on a configurable look-back window, AlignUp! sets intelligent initial constraint defaults, making the system adaptable and efficient.
- Remembered Constraints: AlignUp! carries over constraints from previous lineup scenarios, leveraging yesterday's work to make today's lineup management even more efficient.
- One-Click Assignment Execution: With a simple click, you can set assignments, making the process user-friendly and efficient.
- One-Click Clear All Assignments: AlignUp! allows you to clear all assignments with a single click, providing flexibility and ease of use.
- Integrating Existing Assignments: AlignUp! can integrate existing assignments as constraints, ensuring any specific assignment requirements are considered.
- Minimizing Distance to Start and End Sites: AlignUp! considers the distance between the trucker's location and both the start and end sites of the shift, optimizing travel distance and time.
Recommendation for Management
We recommend that management embrace AlignUp! as a key part of your lineup management process. By adopting this feature, your organization will become more efficient and resilient.
5-Step Implementation Plan
- Explain the Importance: Communicate the benefits of AlignUp! to project managers, dispatchers, and other decision-makers in your organization. Use this newsletter!
- Mandate AlignUp! Use: Require that lineup scenarios be built through AlignUp! to ensure that all of the benefits are achieved by the organization.
- Update Data: If AlignUp! solutions are not correct due to inaccurate trucker location or equipment data, require that the data be updated to maintain accurate and efficient solutions.
- Rotate Dispatch Responsibilities: Implement a rotation of who actually builds and dispatches the lineup to ensure that your process is robust and stress-tested.
- Report Back in Two Weeks: After the implementation of AlignUp!, have the team report back on its effectiveness, allowing for any necessary adjustments to optimize the system further.
Trucking dispatch has long been a source of inefficiency and risk, but no longer. Let's make this a solved problem together.
Regards,
Sean Devine
Founder & CEO, XBE